Machining or metal cutting is one type of secondary manufacturing process by which excess material is gradually removed by shearing from pre-formed blank in the form of chips using a wedge shaped cutting tool to obtain desired shape, size and finish. It is one subtractive manufacturing process, which indicates layer by layer material is removed to get desired form. There exist a large number of such processes—each having different capability and is suitable for specific purpose. Examples of machining processes include straight turning, taper turning, internal turning, threading, facing, centering, drilling, boring, reaming, tapping, planing, shaping, slotting, milling, fly cutting, hobbing, lapping, honing, grinding, etc. Primary intension of all such processes is to obtain intended form having better finish, high dimensional accuracy and close tolerance.
During machining, the cutting tool forcefully compresses a thin layer of material to gradually shear it off. For uninterrupted removal of material from workpiece, certain relative motions between cutter and workpiece are indispensably necessary. Such motions can be broadly classified into two categories—formative motions and auxiliary motions. Simultaneous action of these two motions help obtaining various three dimensional features. Cutting motion and feed motions come under formative motions; while secondary feed motion, depth of cut, indexing motion, relieving motion, etc. come under auxiliary motions. Cutting motion (CM) can be imparted by rotating or oscillating the workpiece or cutter. This CM basically imparts necessary cutting velocity; while feed motion (FM) imparts necessary feed velocity.
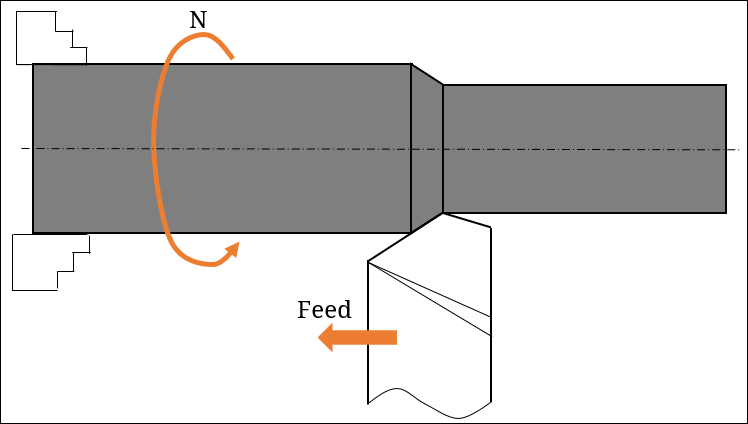
Cutting velocity is most important process parameter in every machining process as it influences a large number of machining responses including cutting force, power consumption, material removal rate, cutting temperature, tool life, etc. It is also one important parameter for analytically estimating all such responses. On the other hand feed rate helps covering up a large area of work surface during machining. A synchronous action of cutting velocity and feed rate helps continuously removing material from a larger area. Feed rate has only little influence on force, MRR, temperature, etc.; however, it directly influences machining time and finish or roughness of finished surface. Various differences between cutting velocity and feed rate are given below in table format.
Table: Differences between cutting velocity and feed rate
Cutting Velocity | Feed Rate |
---|---|
Cutting velocity helps removing a thin layer of material from work surface by compressing it against tool tip. | Feed helps in covering up a larger area during machining by moving the cutter or worktable in intended direction. |
It gives generatrix. | It gives directrix. |
It is commonly expressed in m/min and denoted by Vc. | It is commonly expressed in mm/rev, mm/min or mm/stroke and denoted by s or f. |
It influences cutting force and power consumption in machining. | It has insignificant influence on cutting force and power. |
It has no direct role in deviating chip from orthogonal direction. | In most cases, it influences actual chip flow direction. |
It has greater impact on cutting temperature, tool wear and tool life. | It has comparatively lower impact on cutting temperature, tool wear and tool life. |
It has no direct role in scallop or feed marks generation on machined surface. | Feed results scallop marks on finished surface, which determines primary surface roughness. |
Interaction of cutting velocity and feed rate: During machining, the wedge shaped cutting tool compresses a thin layer of work material and gradually shears it off in the form of chip. A relative velocity between workpiece and cutter is desired to impart the intended compressive force. Cutting velocity actually supplies the primary relative velocity and thus helps in realizing material removal. However, to realize such material removal from entire work surface, the cutter or workpiece (different for different machining operations) must be provided another synchronous motion along the intended direction. This is known as feed motion. Simultaneous action of cutting velocity and feed rate along with other auxiliary motions fulfils basic machining requirement.
Generatrix and directrix: Basic function of machining is to produce various geometrical surfaces with higher accuracy and better finish. Generation of any geometrical surface requires use of generatrix and directrix. These are two line vectors—together they generate intended geometrical surface (flat or curved). These are provided by formative motions between cutter and workpiece. Usually, cutting motion provides necessary generatrix; while feed motion provides necessary directrix.
Units of measurement: Although both express velocity (a derived physical parameter), they are measured in different ways and so their units are different. Cutting velocity is commonly measured in meters per minute (m/min). Sometime, especially with high speed machining, it is also expressed in meters per second (m/s). Cutting velocity differs from cutting speed, which indicates rotational speed of cutter or workpiece and is measured in revolutions per minute (rpm). On the other hand, feed rate is measured in various units for different machining operations. In lathe operations feed is measured in millimetres per revolution (mm/rev); in milling processes mm/flute; in shaping mm/stroke; in drilling mm/rev; and so on. In CNC operations, feed is expressed in mm/min, which is obtained by multiplying the original feed with cutting speed and other parameters (such as number of flutes).
Impact on cutting force and power consumption: These are two important factors in every machining operation. Starting from cutter design, cutter selection, and machine tool performance to material removal rate (MRR), surface quality, and machinability—all depend (directly or indirectly) on those two factors. While machining a particular material using a specific cutter under given conditions, with increase in cutting velocity, cutting force and power consumption also increase. Feed rate also has influence on the same; however, in lesser scale.
Chip deviation angle: Majority of machining analysis is performed assuming orthogonal cutting that is chip flows on the orthogonal plane. However, in most cases, chip does not flow in the orthogonal plane; instead it flows along oblique plane. Restricted cutting effect, cutter nose radius, and inclination angle of the tool separately cause chip deviation from orthogonal direction. Although the deviation angle is small, feed velocity has an impact on the chip deviation caused by restricted cutting effect. On the other hand, cutting velocity has no direct role in deviating chips from orthogonal plane.
Cutting temperature and tool life: Cutting temperature is another crucial factor in machining as higher temperature can severely hamper finished surface quality, can accelerate tool wear and can steeply reduce tool life. Cutting temperature can be controlled by employing optimum set of machining parameters and using lubricant or coolant. Cutting velocity has greater impact in increasing temperature and thus it can be controlled by reducing velocity. However, that may lead to degraded productivity. Substantial portion of heat generates due to intense rubbing of flowing chips with rake surface of cutter. Reduction of velocity will also reduce chip production rate and thus lower heat will generate. High feed rate also causes high cutting temperature; however, its impact is lower as compared to cutting velocity. Life of cutting tool relies heavily on cutting velocity; and also on feed rate and depth of cut in lower scale (can be attributed to Modified Taylor’s tool life formula).
Scallop marks and surface roughness: Scallop marks or feed marks are inherent to machining and is found on finished surface that leads to primary surface roughness. Such undesired marks are produced between two successive passes due to presence of tiny unremoved material. Higher feed rate imparts larger marks and thus surface roughness increases. Thus surface finish can be improved by lowering the feed rate; however, that may lead to reduced MRR and productivity. On the other hand, cutting velocity has no role on generating scallop marks and thus does not contribute on surface finish.
Scientific comparison among cutting velocity and feed rate in machining is presented in this article. The author also suggests you to go through the following references for better understanding of the topic.
- Machining and Machine Tools by A. B. Chattopadhyay (1st edition, Wiley).
- Manufacturing Engineering and Technology: SI Edition by S. Kalpakjian and S. R. Schmid (7th edition, Pearson Ed Asia).